Many 3D scanners use structured light technology, which is both versatile and accessible for consumers. However, the interaction of light with various surfaces can pose challenges. For example, mirrors reflect light away from the scanner’s sensors, often leading to missing or noisy data. Similar issues occur with other reflective or transparent surfaces. In this article, we’ll explore several surfaces and share some effective techniques to overcome these challenges.
Common Difficult Surfaces
- Reflective Surfaces: Surfaces with a mirrorlike finish reflect and scatter the structured light in a way that the 3d scanner’s optical sensors fail to collect data.
Examples: Mirrors, Polished Metal, Glossy Surface Finishes - Transparent Surfaces: Similar to reflective surfaces, transparent surfaces refract and scatter light making it difficult for the 3d scanner’s optical sensors to capture data. Often, built in noise reduction algorithms will automatically delete and erase this noisy data.
Examples: Glass, Clear/See-through Plastic, Opaque materials - Dark Surfaces: Dark colors can absorb too much light, making it hard for 3D scans sensors to detect their own structured light; most 3D scanners have limited light exposure settings and work best with brighter colors.
Examples: Black paint (esp. glossy), Black Materials (i.e. plastic, metal) - Fuzzy/Fluffy Surfaces: Fuzzy and Fluffy surfaces suffer from a combination of different problems due to the small, scattered elements like hairs or fibers, leading to noisy or incomplete scans.
Examples: Hair, Fur, Fuzzy Fabric, Some Foam
For the following situations, not all structured light scanners apply. - Repeating Patterns (Scanner Specific): Some 3D scanners who rely on internal alignment algorithms can become confused if they encounter repetitive patterns in texture or geometry. This can cause critical inaccuracies about the size or shape of the object being scanned.
Examples: Picket Fences, Mesh Filters - Low Feature Surfaces (Scanner Specific): Similarly, low featured surfaces can also confuse a 3D scanner’s alignment algorithms. This can cause critical inaccuracies about the size or shape of the object being scanned.
Examples: Flat uniform Surfaces such as the Floors or a Walls (esp. solid color/no texture), Straight Tubes/Pipes, Vehicle Body Panels
Tips, Tricks, and Solutions
For reflective surfaces such as mirrors and glossy surfaces, here are a few ways to 3D scan them.
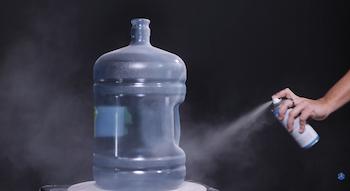
- 3D Scan Spray – Apply a temporary, chalk-like powder to enhance scanability.
Pros: Easy application, some types dissipate over time removing need for cleanup
Cons: Covers the original color, adds complexity to capture the part’s true color - Change Order – Perform the 3D scan prior to polishing or applying surface finish.
Pros: Easier to scan part/surface
Cons: May not reflect the final condition of the part/surface - Dull Surface – Lightly scuff the surface for better light diffusion, though this can alter the surface permanently
Pros: Immediately improvement in scan quality.
Cons: Ruins surface finish. - Adjust Lighting – Dim or diffuse ambient light to prevent overwhelming sensor reflections.
Pros: Simple adjustment
Cons: Benefits are minimal, not always feasible outdoors. - Matte Spray – Replace 3D scan spray with clear matte sprays which help improve scanability while preserving color.
Pros: Easy, captures color and shape more accurately
Cons: May permanently alter the surface. - Other scanning methods – Sometimes, the best case scenario is to try different 3D scanners and combine methods together to get the most accurate part with color. This may involve a multi-leveled approach with scanning the part with a more robust non colored 3D scanner, such as the Kreon, Faro, or Hexagon, and capturing color and texture from a different 3D scanner or from photos, and combine the two in a later model texturing step
Pros: Flexibility
Cons: Complexity - Fuzzy/Fluffy – Try to flatten the fuzz with water or by brushing. Similarly, hair can be brushed and moistened to flatten closer to the scalp.
Pros: Easy to implement
Cons: Not everything can be wet or flattened easily - Add Uniqueness – Add distinctive objects or markers around low-feature or repeating pattern areas to aid scanner alignment. Some 3D scanners require applying targets to the 3D scan area/volume, and they serve a similar purpose.
Pros: Improve accuracy
Cons: Extra preparation and post processing required.
Additional Tips for Success
The above list has a broad range of solutions which we have used successfully in a variety of projects. But sometimes, there are novel problems which require novel solutions. Here’s some additional things that are always worth trying.
- Experiment – Try using the 3D scanner at different angles and distances. Oftentimes having the optical sensor orthogonal to the surface of interest can help reduce the noise the optical sensor can see, leading to better scans.
- Dirty – Leaving a surface a little dirty or dusty is similar to applying a 3D scan spray. If you were planning on spraying a surface on the part anyways, just clean areas which need to be cleaned and let the dust help your 3D scanning process.
- Post Processing – 3D modeling software can be used to help clean up noisy scan data or completely model areas which were unable to be captured. The model can then have texture applied to it from the difficult part.
Conclusion
Difficult to scan surfaces are common and can often lead to frustration and delays. With these solutions under your belt, you can be confident that nothing can stand in your way.
For further insights or questions, feel free to contact us here at Digital scan 3D. We’d be happy to try and help you with your project.
Additionally, if you want to see a video presentation on this same topic, check out our YouTube video here: