Reverse Engineering
Reverse Engineering Services
Reverse Engineering (3D Scan based) is the process of reproducing a part by extracting surfaces or sketches from a scanned point cloud/mesh to create a CAD model of the part. Different methods are used either prismatic/mechanical or organic. The product reflects how the part was to be designed originally. Creating a 3D CAD model from a 2D drawing to reflect design intent is also another form of reverse engineering. Reverse engineering is becoming a more popular method of creating a 3D model of a part without existing CAD files. This process has saved lots of individuals and companies’ time, cost and increased quality on design processes and time to market.
A 3D scanner can be used to scan/analyze a real-world object or environment to collect data on its shape and possibly its appearance (color or/and texture). The collected data can then be used to construct a digital 3D model.
Digital Scan 3D (DS3D) has trained staff that will help and recommend the best reverse engineering package for your application. Reverse engineering process falls into three major categories:
1. Free-Form or Organic Parts
2. Prismatic or Mechanical Parts
3. Hybrid Modeling
The reverse engineering process used to reverse engineer an object will depend on whether a part is organic or prismatic. If you have any questions, please contact us.
Range of objects we can 3D Scan
Accuracy we can keep/delivery
Project Delivery – (ETA)
Reverse Engineering
Reverse Engineering QA/QC
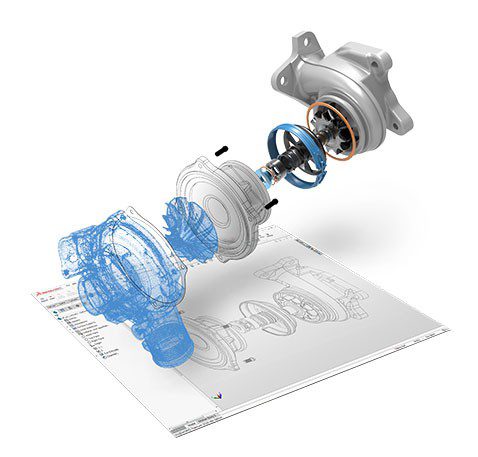
CAD File
Final reverse engineered model. This CAD file can be modified or exported as a .STEP/IGES/Parasolid or any native software file such as SolidWorks, NX, and any other common CAD packages (STEP/IGES/SolidWorks).
CAD Software to modify and complete Design intent: