In today’s day and age, the race for quality has been paramount to a company’s success. In the past, companies gave little attention to standardized quality, and a product’s quality often relied more on the skill and performance of the individual factory worker and less on some overall product standard. With the introduction of programs like six sigma, quality assurance (QA) and reduction of waste and rework on a production line became very important, paving the way for more rigorous quality control. With metrology switching to highly sensitive touch probe CMMs, manufacturing could reach unparalleled quality standards than prior. Now, with 3D scanning, a new frontier of possibilities is available for ever tightening quality assurance standard on more complex parts.
In this article, we’ll first explore why one may want to use 3D scans for QA, then we’ll look at different methods of 3D scanning and what capabilities they have for QA, and finally we’ll end with some examples of how 3D scanning is implemented in various industry sectors for QA purposes.
Why 3D Scan for Inspection?
Traditional manufacturing metrology techniques often relied upon the simple contact or touch probe. A probe works by being moved in a known direction until it makes contact, or “touches”, the part within the workspace. By comparing these contact points with a drawing or CAD model, a physical representation of the part in the workspace can be generated. These contact points, or just points, together make up what is called a Point Cloud. These point clouds can then be used for a host of downstream processes such as inspection, reverse engineering, or even 3D printing.
With the introduction of 3D scanning the point cloud could be made much quicker, more complete, and without concern for touching the part in the workspace. The QA teams can then inspect these more complete point clouds, allowing them to find potential issues quicker, and easier. A point cloud with more information is usually referred to having higher resolution. A higher resolution point cloud allows the big picture to be seen as well, opening up the possibility of discovering an issue even if it was not originally within the scope of the original inspection.
In this way, 3D scanning for inspection can save time and money. Potential out of scope issues can be found easier and resolved as well.
How to 3D Scan
There are a few different forms of 3D scanning. The most common forms of 3D scanning are structured light, laser scanning, and photogrammetry. These different forms of 3D scanning offer different benefits. While there are different methods and technologies behind 3D scanning, such as time of flight, phase shift, and triangulation methods, we are more focused on the generalized methods of 3D scanners which we mentioned above. Some are well suited for QA purposes, while others may not be as ideal. We will look at these different categories of 3D scanner methodologies and weigh their usefulness for quality purposes.
Structured light
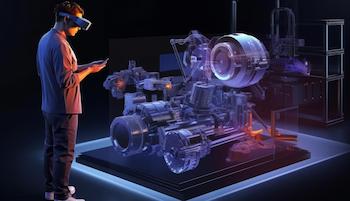
Structured light refers to using a controlled light source, often produced by the scanner itself. When the scanner senses distortions in the reflected light, its software analyses and interprets the light to produce a cloud of accurate points in space which would then form a point cloud representation of the object being scanned. Light of a known wavelength is used, allowing the sensor and software to be optimized for sensing that wavelength, increasing accuracy and reducing noise in the scan.
With some options like the fully wireless Artec Leo, structured light scanning can be very portable. Structured light scanning is accurate, has a high output resolution, and in most cases, can support a texture output. However, it can be limited by equipment specific focal lengths, and so is only advisable for small to medium sized parts for QA inspections.
Laser scanning
Laser scanning uses lasers, visible and invisible, and detects their deflection and reflection into a sensor. Similar to how structured light works, only that it usually uses only one laser or light line at any given point. A sub category of laser scanning is LiDAR scanning, which shoots a laser at an object and calculates the time difference between the laser shot and detected reflection.
Laser scanning tends to be more accurate, has a medium* output resolution, but rarely includes a texture option. While typical laser scanners have a similar focal range issue, in combination with a CMM arm or similar setup, they can be used for larger applications. Also, LiDAR scanners have relatively long ranges in contrast, with possible measurements being possible 100+m (328+ft) or more away from the scanner. However, laser scanning typically requires targets or at least its own known coordinate system, so additional setup may be required depending on equipment. With this in mind, laser scanning is usually a great option for large parts where having a common coordinate system is critical, however, it is still a great option for small and medium sized parts as well.
Photogrammetry
Photogrammetry is one of the easiest types of 3D scanning to start with. Photogrammetry is the process of taking reliable measurements for photographs. While professional grade equipment is not required, it definitely helps with accuracy and data quality. In order to create a proper 3D model with photogrammetry, multiple photos of the same part would need to be taken from different angles. By identifying common points and features in photos, a 3D model can then be created. Also, it is important to include reference parts or have targets and scale bars included with the part in the photos to increase accuracy. Depending on the camera available, the 3D
scan texture can be leagues better than a typical 3D scanner. Since cameras can relatively easily change lenses or focal lengths, photogrammetry can be very helpful for very large projects.
With this in mind, photogrammetry tends to be a little time consuming. The parameters required to correctly triangulate information from multiple images can be tedious to record unless one has professional equipment. Photogrammetry tends to have medium accuracy, low resolution, but high texture quality. With enough photos, you can increase the point cloud resolution, but some things like trees can end up giving a lot of noise, keeping the accuracy about the same. It is not as ideal for smaller part QA purposes typically but can be great for other applications.
Implementation of 3D Scanning for Quality Assurance (QA)
Using a 3D scanned point cloud for QA can be applied in many different scenarios, across the entire length of a products development. From the early stages, a clay model can be 3D scanned and reverse engineered, using digital tools to smooth out any human imperfections in the clay, ensuring a quality model. Next, rapid prototyping can use 3D scans to inspect and validate iterative designs. Once the part is being mass produced, 3D scans can be used for dimensional inspection and defect detection. And finally, 3D scanning can be applied to an automated inspection workflow with parts being scanning automatically in a robot cell with little to no human interaction.
Reverse Engineering
Reverse engineering can be accelerated by modeling based on an existing model, and using a 3D scan to bring a point cloud representation of the model directly into your modeling interface. Popular tools like Oqton’s Geomagic Design X allow a user to not only model based off the scan data, but also do a quality validation to ensure no feature is forgotten in the modeling process
Rapid Prototyping and Iterative Design Validation
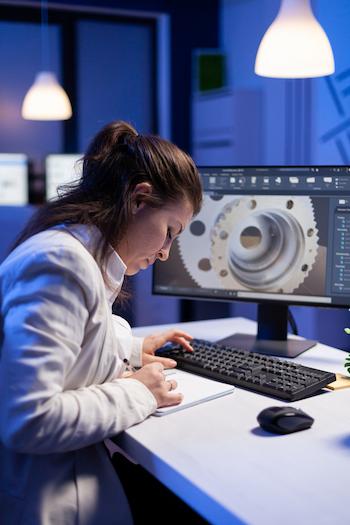
One can use a 3D scanner to scan an area where a part needs to be designed for. For instance, an assembly where a prototype needs to be able to fit, function, and not interfere with the existing assembly. By 3D scanning the assembly, the prototype can be installed and tested digitally, saving time by reducing the number of revisions and speeding up the time to market by ensuring it to be a quality design from the start.
Dimensional Inspection and Defect Detection
Similar to what metrology teams currently do on a production floor, part samples can be collected and inspected, looking for and solving quality issues before they leave the factory. Using a 3D scan can help speed up the data collection process, and provide a big picture view of the part, allowing potentially hidden issues to become visible.
Automated Inspection
And finally, having an automated inspection cells throughout the production floor using 3D scanners allows a quick snapshot of quality as the product moves through the assembly line. Tool wear and machine failure can be detected by watching trend lines based on these scanned inspections.
Conclusion
Implementing 3D scanning into your quality assurance workflow can help tremendously. From ensuring new ideas meet design requirements from the start, to early detection of failure and potential issues, using a 3D scan can give a big picture view that other measurement tools may not be able to give. Between the different capabilities of structured light, laser light, and photogrammetry, all types of QA at various levels can be achieved, ranging from small parts to massive construction sites.
In this way, modern QA teams should be aware, and learn the capabilities of 3D scanning and how and when to use it in their workflow.