Introduction
Across industries like aerospace and medical, generating CAD models from 3D scan data is vital for producing high-quality designs in product development. However, many CAD programs struggle to handle raw 3D scan data, which often consists of dense point clouds. These programs are typically optimized for precise modeling rather than processing millions of data points. To bridge this gap, raw scan data must be converted into mesh files, which can then be used to create CAD models—a process commonly known as reverse engineering.
At Digital Scan 3D, we specialize in high-precision 3D scanning and reverse engineering, guiding companies through the process of transforming 3D scan data into CAD models. This guide provides a clear, high-level overview of the steps involved, highlighting the tools and techniques used at each stage to ensure a seamless workflow.
Step 1: Capture Quality Scan Data
The initial and most critical step in the process is collecting raw scan data. If this step is rushed or the resulting data lacks quality or resolution, every subsequent stage will be compromised. Higher accuracy in the scan directly enhances the efficiency and success of the reverse engineering process.
Types of 3D Scanners
A variety of different 3D scanners are available depending on the project.
✅ Handheld 3D Scanners – Highly Flexible and maneuverable.
✅ Stationary 3D Scanners – High accuracy and resolution capabilities.
✅ Industrial CT Scanners – Able to 3D scan internal structures or complex geometries.
Methods of 3D Scanning
✅ Laser/Structured Light Scanners – Most common with handheld 3D scanners. Constrained to operation within a focal range for the optical sensor.
✅ Lidar & Photogrammetry – Best when the scanned size is considerably large such as buildings or landscapes.
✅ CT/X-Ray – Expensive, but is capable of scanning internal structures.
Key Factors to Observe While Scanning
Achieving high-quality 3D scan data requires careful attention to several key factors:
- Environment – Ensure the object is scanned under suitable ambient lighting to maximize data quality. For larger objects, clear ample space around them to allow the scanner to move around to capture data from multiple angles, ensuring comprehensive coverage.
- Surface Preparation – Certain surfaces can pose challenges for 3D scanners, leading to noise or unwanted reflections. Proper preparation minimizes these issues, enhancing scan accuracy. For detailed guidance on preparing challenging materials, explore our blog: Useful Tips and Tricks for 3D Scanning Challenging Materials.
- Equipment Settings – Adjust your scanner’s settings to capture fine details effectively. Optimal settings will vary depending on your specific hardware, so tailor them to the object’s complexity and requirements.
At Digital Scan 3D, we provide advanced 3D scanning services and solutions, delivering high-precision scan data tailored to your industry’s unique needs.
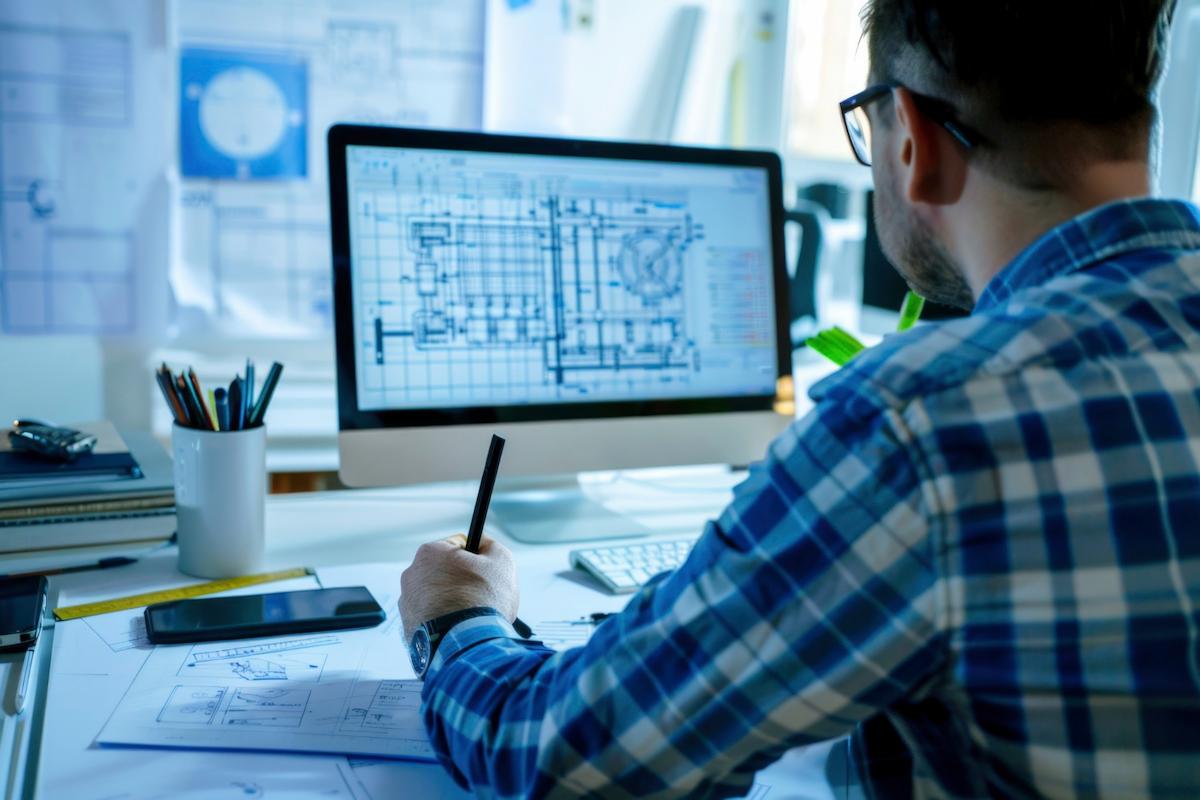
Step 2: Converting Raw 3D Scan Data for Reverse Engineering
Raw 3D scan data is typically stored in a device-specific point cloud format, which can be readily converted into universal point cloud formats like PLY, XYZ, or ASC. For reverse engineering purposes, however, transforming the raw data into a mesh format—such as STL or OBJ—is ideal, as these formats are better suited for creating CAD models.
3D Scan Data Processing Software
Most 3D scanners come with proprietary software that enables technicians or engineers to convert raw 3D scan data into a usable mesh file. However, depending on the scanner software’s capabilities, further refinement of the mesh may be necessary. In such cases, secondary mesh-editing software is required to enhance or complete the mesh processing.
Below are examples of scanner-specific software designed to convert raw 3D data into mesh data:
- Artec Studio (For Artec 3D scanners)
- Zenith (For Kreon 3D scanners)
- VXelements (For Creaform 3D scanners)
If additional mesh editing is needed, the following programs are commonly used for refining 3D mesh data.
- MeshLab
- Blender3D
- Autodesk Meshmixer
- Geomagic Design X (Mesh editing tools)
Cleaning Steps
To prepare 3D scan data for reverse engineering or CAD conversion, follow these key steps to ensure a clean and accurate mesh:
✅ Remove noise and outliers – Eliminate unwanted points, artifacts, or irrelevant data from the scan. Many software tools offer automated features to detect issues in the mesh and suggest repair solutions, streamlining the cleanup process.
✅ Align and merge multiple scans – For complex objects requiring scans from multiple angles, properly align and combine the scans to create a complete dataset. Accurate alignment is critical to capturing the full geometry without gaps or overlaps.
✅ Fill holes and repair defects – Address any gaps or imperfections in the mesh. While not all reverse engineering workflows require a watertight mesh, creating one can improve compatibility with CAD software, as most CAD models are watertight. Thoroughly inspect the mesh for missing data, especially in critical areas, as additional scanning may be needed. It’s easier to collect more scan data at this stage—when the original object is typically still accessible—than later in the reverse engineering process. Missing data could lead to incomplete or inaccurate elements in the final CAD model.
✅ Check for Tesselation and Alignment Issues – Review the mesh for tessellation errors (e.g., non-manifold geometry or overlapping triangles) and alignment problems. While modern mesh-generating software minimizes tessellation issues, poor alignment between scans can cause errors, such as visible seams or steps where scans overlap. These issues are often noticeable at the boundaries of merged scans and should be corrected to ensure a smooth, accurate mesh.
Step 3: For Converting 3D Scan Data to CAD Model
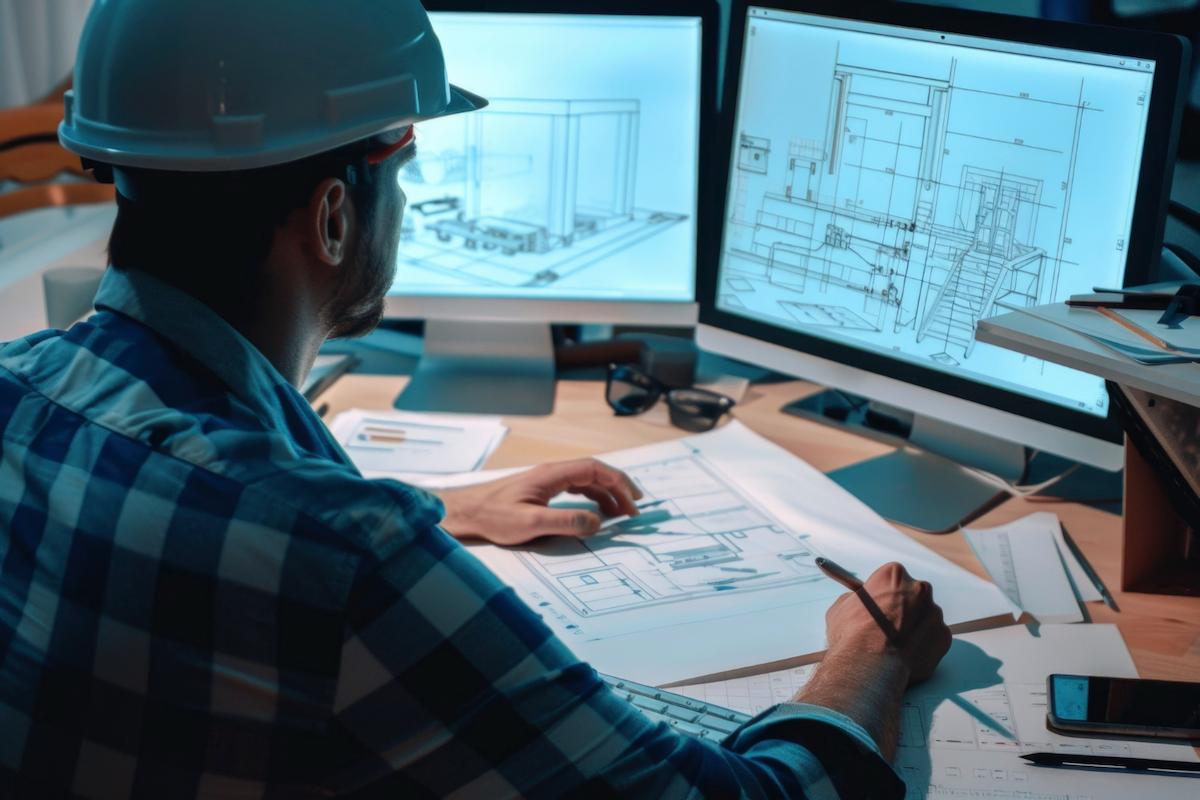
Once the 3D scan data is cleaned and prepared, the reverse engineering process can begin. Before starting, it’s essential to define the design objectives, as different modeling approaches are better suited for specific applications. These approaches can be broadly divided into two categories: Organic Modeling and Prismatic Modeling, with Hybrid Modeling combining elements of both.
A. Organic Modeling – Exact Fit Surfaces
Organic modeling is ideal for freeform, natural shapes, such as prosthetics, medical models, vehicle exteriors, or sculptures. It typically relies on NURBS (Non-Uniform Rational B-Splines) modeling to create smooth, precise surfaces that closely match the scanned data. Many software packages offer automated tools to streamline this process. For instance, Geomagic Design X features AutoSurface, a proprietary algorithm that generates NURBS surfaces automatically directly onto scan data. Other programs such as Creaform VXmodel and Rhino provide similar NURB tools for rapid surface creation. NURBS-based organic modeling ensures a near-perfect fit to the original scan, making it suitable for applications requiring high fidelity to the scanned object.
B. Prismatic Modeling – Machined Parts
Prismatic modeling is best for mechanical components with well-defined, geometric features, such as flat faces, edges, or cylindrical shapes. This method uses sketches, extrusions, and other CAD operations to create an idealized model, often ignoring imperfections like pitting, rust, or wear captured in the scan data. Prismatic modeling can reconstruct missing or damaged areas by inferring design intent, though this requires active decision-making by the user. In tools like Geomagic Design X, automated region-based tools can accelerate the workflow. Since most CAD software is built around prismatic modeling principles, this approach is typically the easiest to learn and apply.
C. Hybrid Modeling – Combining Strengths
Hybrid modeling combines organic and prismatic techniques to leverage the strengths of both. It enables automated exact-fit surfaces for organic shapes alongside precise prismatic features for mechanical parts. This approach is particularly useful for creating components within larger assemblies, reducing the need to manually model every element prismatically. Hybrid modeling balances speed and accuracy, making it versatile for complex projects.
Step 4: Refining & Optimizing the CAD Model
During the reverse engineering process, users must carefully review each step to ensure the resulting solid or surface CAD model meets specified tolerances. Most leading reverse engineering software supports importing 3D scan data as a reference, enabling modelers to compare and refine their CAD models against the original scan for accuracy and completeness.
🚩 Verify accuracy: Tools like Geomagic Design X’s Accuracy Analyzer provide heatmaps and metrics to evaluate model smoothness, dimensional accuracy, and other parameters. These features allow users to confirm that the CAD model aligns precisely with the 3D scan data, identifying and correcting deviations to meet tolerances.
🚩 Address Missing features: Using 3D scan data as a reference helps modelers quickly spot discrepancies, such as missing or incomplete features in the CAD model. By visually comparing the model to the scan, users can rectify these issues, ensuring the final model fully represents the scanned object.
🚩 Design for Manufacturing (DFM): CAD models should be developed with the intended manufacturing process in mind. If the 3D scan is derived from an existing physical part, it likely reflects a design optimized for a specific process, such as machining or molding. While additive manufacturing (AM) offers new design possibilities, users should prioritize cost-effective and optimized manufacturing methods to align with DFM principles, balancing innovation with practicality.
Step 5: Exporting the CAD Model for Use
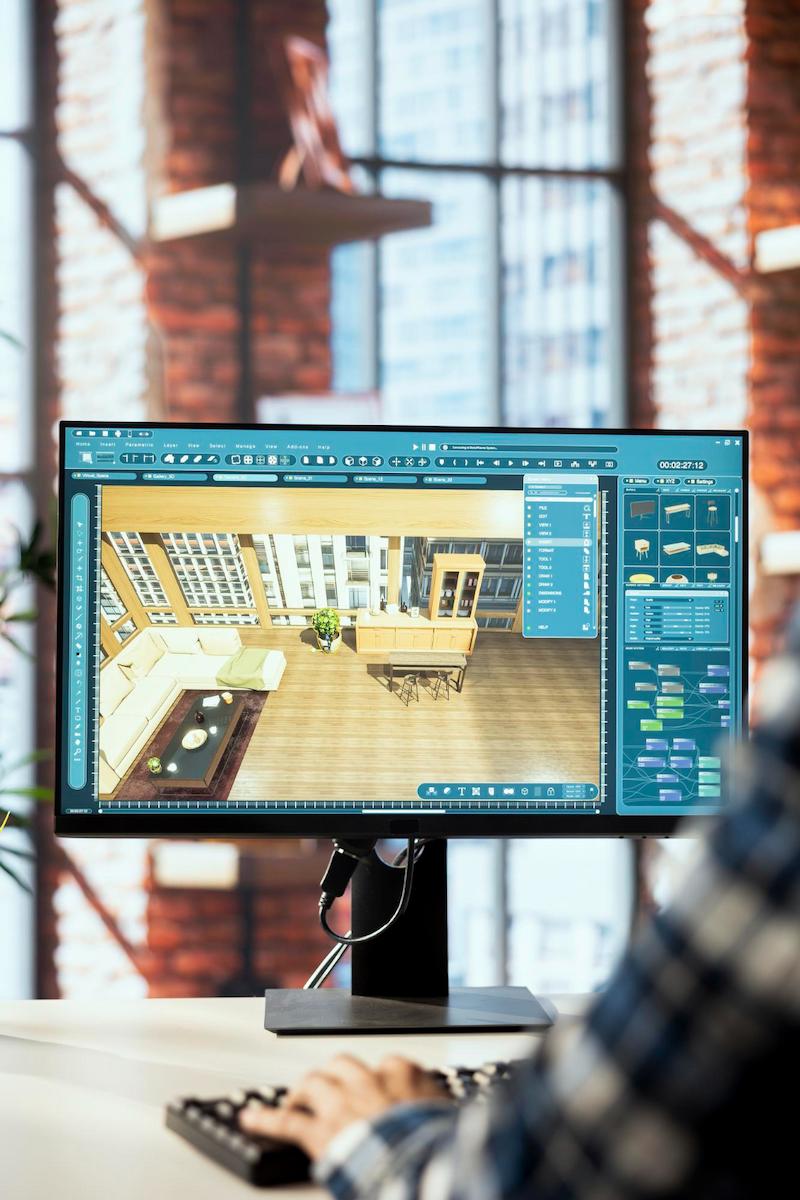
The final step in the reverse engineering process is exporting the CAD model into a file format suitable for its intended use. Different manufacturing programs require specific file formats for programming machining paths, while others support a range of formats. Selecting an appropriate file format ensures the reverse-engineered CAD model is compatible with downstream workflows.
Common CAD Formats:
- These widely accepted formats are compatible with many programs but are “dumb” files, meaning they lack parametric data and are harder to edit later. Examples include:
- .STEP/.STP – A near-universal format, ideal for compatibility across most CAD software.
- .IGES/.IGS – Best suited for surface models, particularly for older CAD system.
- These formats retain the full parametric history of the CAD model, making future edits easier. Examples include:
- .SLDPRT (SolidWorks)
- .PRT (Siemens NX)
- .CATPart (Dassault Systèmes CATIA)
Choosing the right format depends on the manufacturing requirements and whether future modifications are anticipated, balancing compatibility with editability.
Conclusion
The journey from a 3D scan to a reverse-engineered CAD model is a streamlined yet powerful process that transforms physical objects into precise digital designs. It begins with capturing measurements using a 3D scanner, which generates raw data in the form of a point cloud or mesh. This data is then processed and refined into a high-quality 3D mesh file, serving as a reference for constructing a CAD model. This versatile workflow supports a wide range of industries, including automotive, aerospace, medical device manufacturing, and product design, enabling applications from recreating complex vehicle components to designing custom prosthetics.
To achieve optimal results, selecting the appropriate modeling approach is critical:
- Organic Modeling: Ideal for freeform shapes like sculptures or medical models, this method often uses automated surfacing tools, such as Geomagic Design X’s AutoSurface or Creaform VXmodel’s NURBS generation, to create smooth, exact-fit surfaces that closely match the scanned object.
- Prismatic Modeling: Best suited for mechanical parts with defined geometric features, this approach reconstructs idealized CAD models, compensating for imperfections like rust or damage in the scan data. Tools like SolidWorks or Autodesk Inventor excel in creating machinable designs.
- Hybrid Modeling: Combining the precision of prismatic modeling with the flexibility of organic surfacing, this approach enables high-accuracy modeling for complex assemblies, balancing automation and manual control.
Each method ensures the resulting CAD model meets stringent tolerances, with tools like Accuracy Analyzers in leading software providing heatmaps and metrics to verify dimensional accuracy against the original scan. Additionally, Design for Manufacturing (DFM) principles guide the process, ensuring the CAD model is optimized for the intended production method—whether machining, molding, or additive manufacturing—while balancing cost and efficiency.
At Digital Scan 3D, our team of experts is dedicated to guiding you through every step of this process, from scanning to CAD delivery. Whether you need to reverse-engineer a single component or develop a comprehensive 3D solution, we tailor our approach to your unique needs. Contact Digital Scan 3D today to speak with a representative and discover how our cutting-edge 3D scanning and reverse engineering services can bring your projects to life with precision and efficiency